Now, our country’s automotive mould industry is developing rapidly, but the talent and technology in areas such as mould designers are not keeping up. In terms of seeing all the headache of rebound, there is no one who dares to say that they can perfectly solve the problem of rebound, but this problem has always existed, and is a topic we need to discuss properly.
The Material of automobile stamping die
The car structure is complex, there are many kinds of parts, there are many different strength of the stamping parts on the car, from ordinary plate to high strength plate, different plates have different yield strength, the greater the yield strength of the plate, the more likely to rebound.
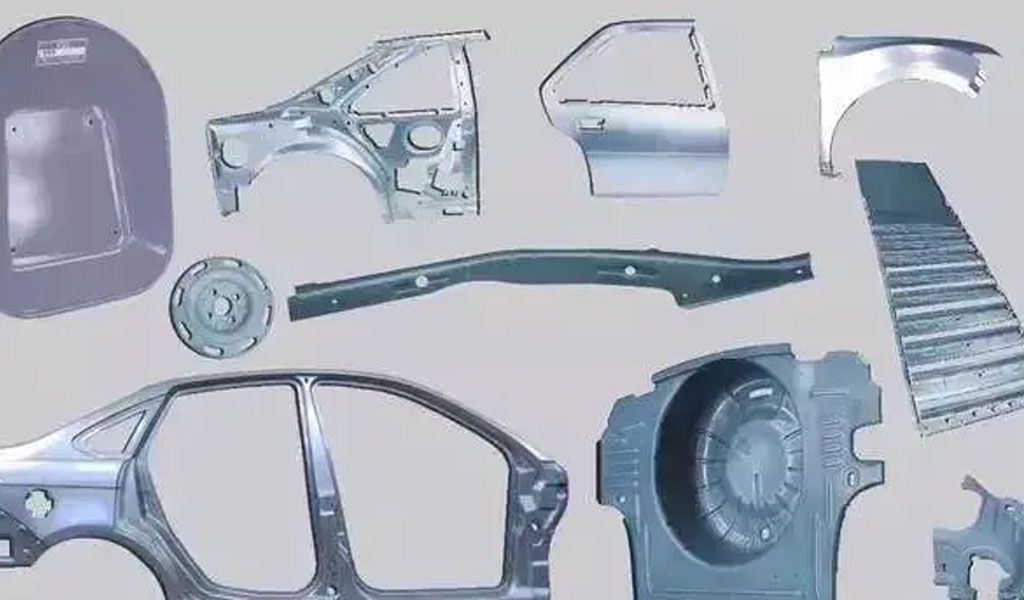
Thickness of automobile stamping die material
As the thickness of the material changes, the rebound phenomenon changes accordingly, mainly because as the thickness of the material changes, plastic deformation becomes difficult, resulting in less rebound.
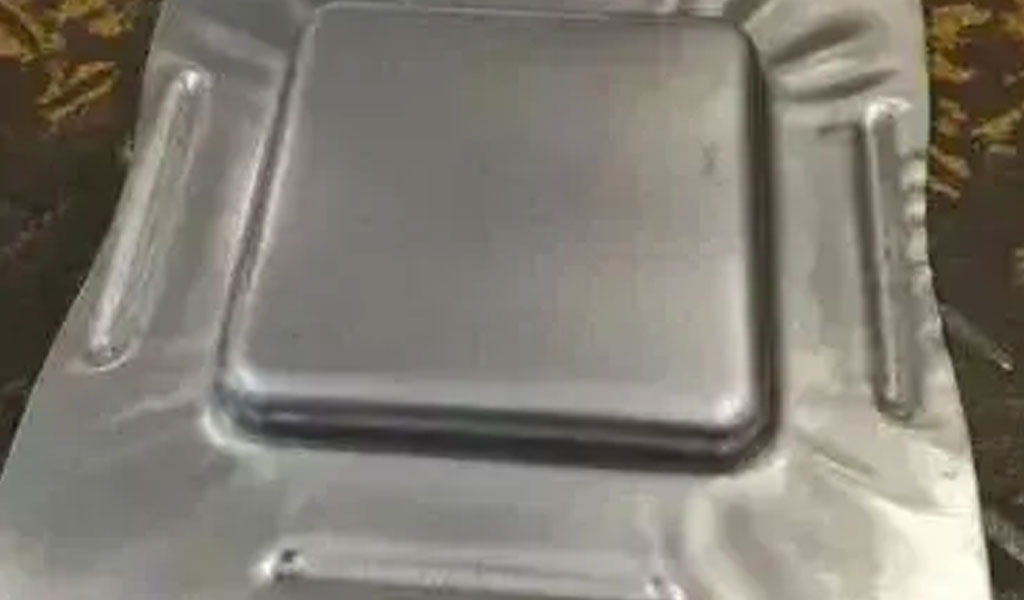
The shape Of automobile products
Different products also have different rebound, the shape of complex products will basically have a step shaping, to prevent the formation of the rebound, there are some special products are more likely to rebound, such as U-shaped products, therefore, in the analysis of forming, we must think about rebound compensation matters.
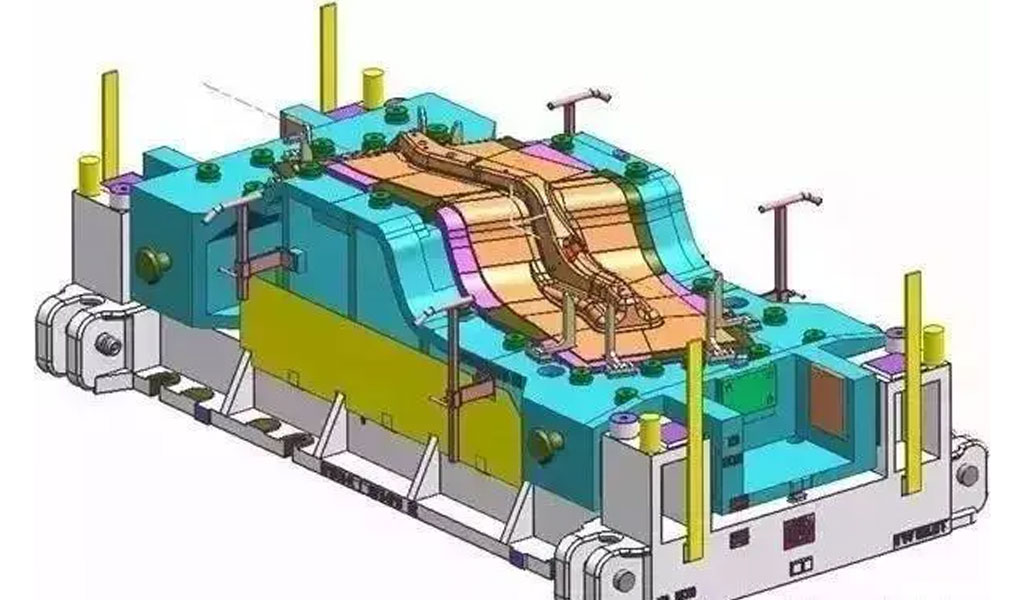
The crimping force Of automobile products
Crimp force plays a vital role in forming. By adjusting the amount of crimp force, the direction of material movement can be adjusted and the internal stress distribution of the material improved. An increase in the crimping force allows the product to be more fully drawn, especially at the side walls and R-angles of the part, which, if fully formed, will increase the stress difference between the inside and outside, thus reducing rebound.
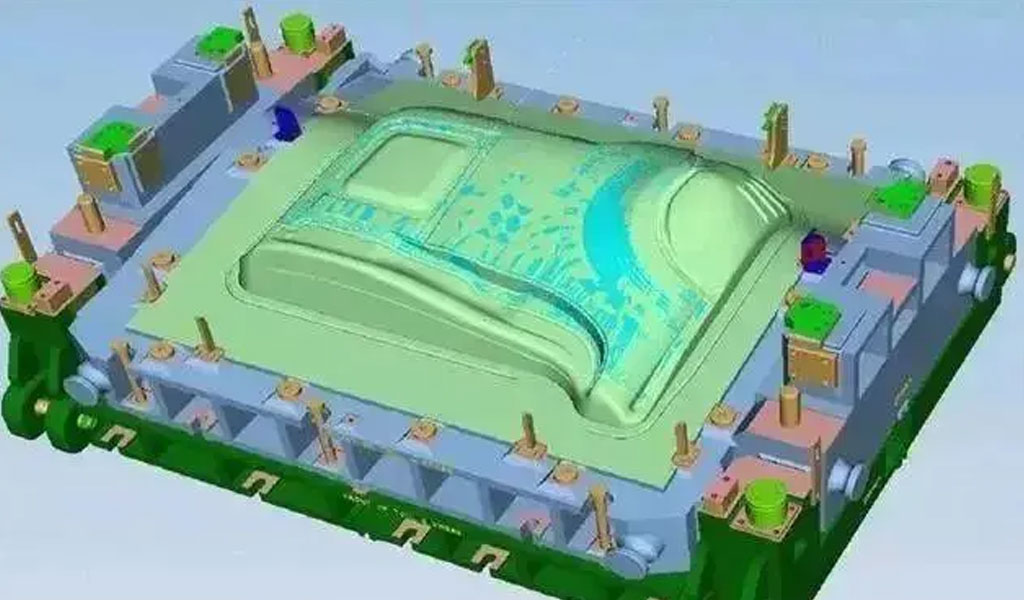
The Stretching bars Of automobile products
The pulling tendons are more commonly used in today’s process. A reasonable setting of the position of the pulling tendons can effectively change the direction of material activity and effectively distribute the material resistance on the press surface, thus improving the material formability, and setting the pulling tendons on the parts prone to rebound will make the parts more fully formed and the stress distribution more uniform, thus reducing rebound.
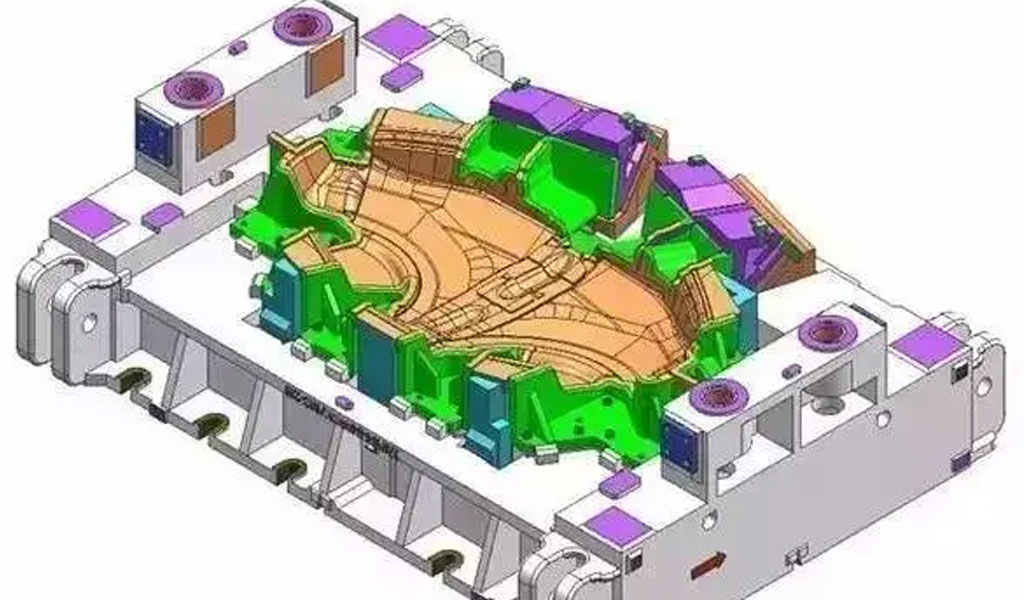